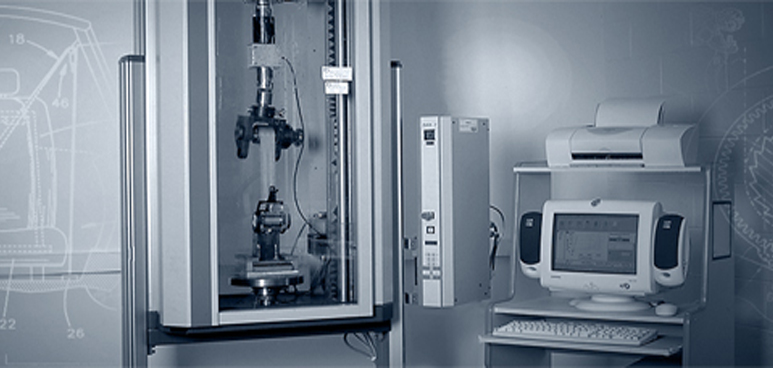
Mechanical Testing
Tohama is a private company was established in Iraq / Basra …. (registration No.000087161- 02 ) providing destructive DT and non-destructive testing NDT and inspection activities throughout qualified inspectors and technicians staff ASNT (American Society for Non-destructive Testing) level ll . They have more than twenty years experience in inspections jobs in many locations and fields, like: rehabilitation for steel structures of the main three bridges in Basra, power plants ,high pressure boilers , main steam lines, they do inspection for most fixed and rotated equipment in a chemical and petrochemical plants such as pressure vessels , heat exchangers, tanks, ,heaters, reformers, separators piping , pipelines, ,valves, safety valves….etc. vacuum and pressure leak testing accordance to related standards and client specification requirements .Our team deals with many types of materials in industry ,carbon steel, low alloy steel, stainless steels….. and they have a good experience more than nineteen years in execution stress relieving PWHT for welding joints ( for piping and their components , pressure vessels and tanks ). Tohama staff have inspectors that executing NDT inspections on rotary equipments like pumps ,rotors ,compressors, fans ,turbines ,gears and capable to check dimensions , run out ,tolerances ,clearances and alignment…etc.